Greenhouse company appears to solve labour shortage with automation
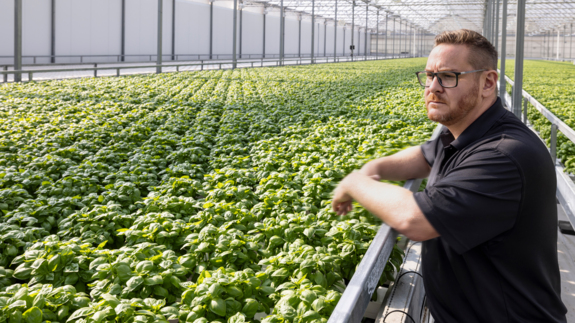
Charles Verdy launched a plan in 2021 that would double his agricultural operation’s production area, confident there was a growing market for his fresh herbs. He was less confident, however, that he would find the workers to help him fulfill this bold expansion.
Verdy is president of Gourma, which operates greenhouses in Saint-Norbert, Quebec, an hour east of Montreal, and distributes a variety of fresh herbs throughout the province. His company had answered the province’s post-pandemic call for more homegrown produce by coming up with a plan to expand the number of its greenhouses.
But the labour shortage got in the way of those plans.
He’s not alone in having difficulty finding workers. According to a 2023 report from Food Processing Skills Canada, the Canadian food and beverage manufacturing industry will need 142,000 new people, or almost 50% of that year’s workforce, in the next seven years. The fact that Gourma is located far from an urban centre makes hiring even more challenging.
Verdy realized that if he wanted to expand and optimize the company’s processes, he could not rely on existing hiring practices and production methods. It was time to turn to automation.
But fresh herbs and automation are not always an easy match. Each of Gourma’s 34 different varieties has its own unique characteristics, such as size and growth time, so it was unrealistic for the company to automate the production of all its plants.
He decided to limit automation to basil, the company’s most popular product.
While the seeding stage of the basil plants was already automated, employees were still placing seedlings on a tray and then moving to the different sections of the greenhouses at every subsequent stage. At harvest time, they had to go into the greenhouses to pick the plants, package them one by one and transport them to a workstation, where other employees would pack them in cases.
While the company could look to machines to automate that part of the process, it would still be tricky. Handling basil plants can be problematic: there is the risk of contamination, and the plants have delicate leaves.
“Customers don’t want damaged plants with torn-off or crushed leaves,” Verdy says.
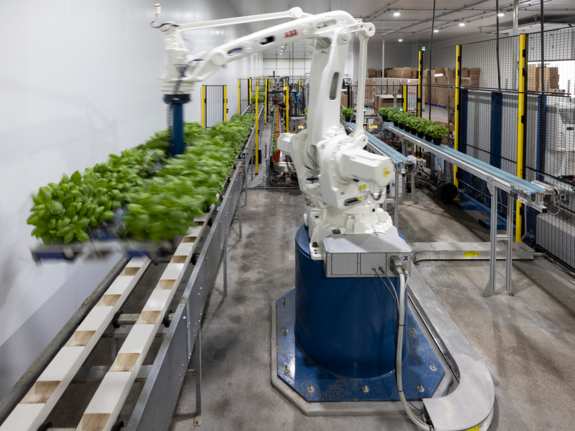
An engineer by trade, the company president understood the concepts and technical jargon involved in the project, but he’d never carried out such extensive automation and needed some support.
He turned to BDC, which helped him prepare specifications, develop acceptance tests for equipment, anticipate pitfalls and avoid foreseeable problems. “They also helped accurately pinpoint my needs and the associated costs,” said Verdy.
Automating basil plant production led to significant productivity gains for Gourma, with the highest achieved in the packaging stage. Machines, overseen by three employees, now handle the following operations:
- bagging the plants
- assembling boxes
- putting the plants in boxes
- sealing the boxes
The results have been very positive, with the robots and conveyor belts helping Gourma to:
- reduce plant damage
- improve time to shelf
- optimize workspace
- increase productivity
- expand to new market
- offset hiring needs
“Switching to a more automated production did not lead to any employee layoffs,” Verdy says. ”but it did help us overcome our recruitment challenges.” Gourma had 12 employees assigned to basil before doubling its production area. After the expansion, it would have needed 25 employees to meet its new capacity demands. “Thanks to the automation project, we now only need four,” Verdy says.
Those freed-up employees were reassigned to the production of other plants, allowing the company to retain its entire staff. This not only enabled Gourma to overcome its staffing challenges but also diversify the work of its teams.
While his employees are on board with the changes, Verdy was careful to include them in the process. He saw them as the production experts and recommends that other businesses looking to automate do the same.
“Their knowledge is crucial, and without their input, a project like ours would have been impossible to carry out. You need to involve them in the project’s development and in implementing new activities.”
He says including your team from the start helps to:
- ensure that proposed solutions are pragmatic and feasible
- attract innovative ideas from staff on the ground
- anticipate or even resolve potential issues
- foster buy-in and commitment among your employees
Experts see resistance to change stemming from fear and pins the blame for that fear on a company poorly communicating its objectives. That was an important issue for Verdy.
“You need to explain what you want to achieve. In our case, we emphasized that we wanted to improve how we work, and that robots would work side-by-side with our team members, not replace them.”
Gourma also listened to its team members to better understand what they needed and wanted. “Everyone’s different,” explained Verdy. “So, we worked with our team members to place them where they wanted to be: those that preferred manual work were given a manual position in the production of other plants.”
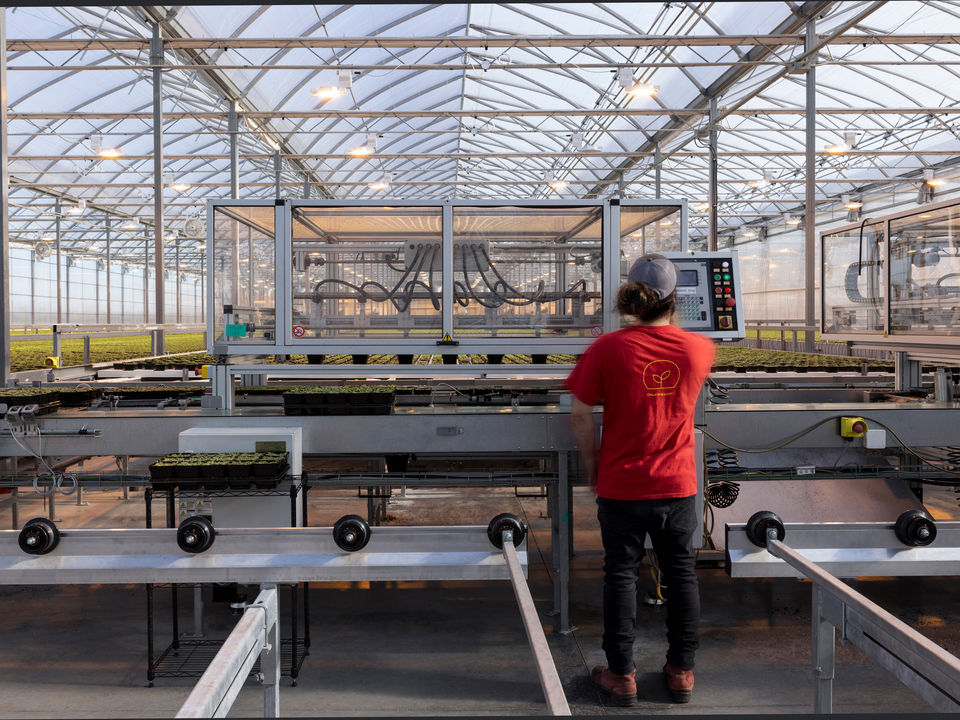
Introducing new processes and technology requires learning new skills. Gourma had to ensure employees had the necessary expertise.
“We provided training with the manufacturers of our new machines as well as with the technology integrator,” said Verdy. Identifying champions—people who are interested and have the potential to develop the skills required for the new positions—helped support the transition.
Gourma now boasts over 20,000 square metres of greenhouses, 65 employees and a more productive operation. “For our entire plant production system, our automation project yielded an increase in productivity of at least 15%,” declares Verdy.
He is no longer worried about finding enough workers, with all the original workers who remained with the company now on board with the changes.
“Today, our employees are so familiar with the technology that they can teach our integrator new things,” said Verdy. “It was a major success.”
Next step
Discover how to leverage robotics and automation in your business by downloading BDC’s free guide, Harnessing the Power of Industrial Automation and Robotics.