PDCA (plan, do, check, act)
The plan, do, check, act (PDCA) methodology is one of the main tools used by professionals to test improvements and manage change for businesses that pursue continuous improvement.
Also known as the PDCA cycle, it offers a simple means for business leaders to plan for new changes, evaluate their performance and make necessary changes once they have been implemented. The cycle can be used in a variety of contexts, from business processes to product development.
At its core, PDCA is a process-improving method that involves a continuous loop of planning, doing, checking and acting. Each stage contributes to the goal of identifying which processes work and which need further improvement.
This approach can be applied to:
- new projects
- process, product or service improvements
- repetitive work processes
PDCA encourages businesses to continually improve in order to stay competitive. By planning, executing, evaluating, and refining processes, businesses can enhance efficiency, effectiveness, and overall performance.
The 4 elements of the PDCA cycle
Plan
This initial stage determines the goals for a product or process and identifies the necessary changes required to achieve these goals. It is here that problems are defined, analyzed, and prioritized. The collection and analysis of relevant data are crucial to planning effectively.
Do
This phase involves executing the planned actions on a small scale and applying the proposed solution or change.
Check
This third step involves evaluating the results of the implemented changes. Expected results are compared with actual results to assess performance and see if objectives were achieved.
Act
The final stage is about learning from the checking phase and acting accordingly. If the checking phase reveals that the changes were successful, they are then standardized and stabilized. If they’re not, the cycle begins again with further planning.
It's important to note that PDCA isn’t a one-time process but a continuous loop. After the acting stage, the cycle reverts to the planning stage, fostering continuous improvement.
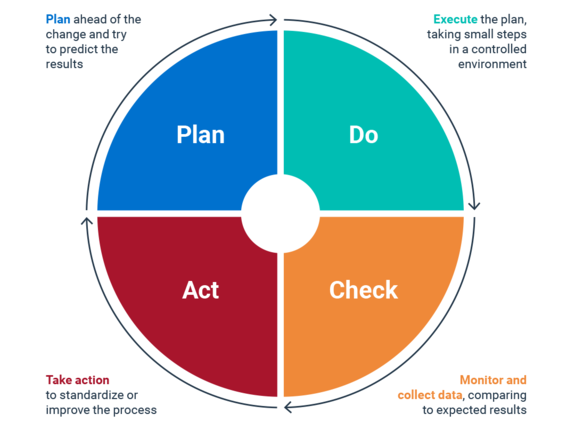
Benefits of using PDCA in business
PDCA offers several benefits when applied in a business situation:
- Continuous improvement: PDCA encourages an ongoing pursuit of process enhancement and a culture of continuous improvement.
- Risk management: By testing changes on a small scale, organizations can identify and mitigate potential risks.
- Increased efficiency: The systematic approach helps to identify inefficiencies, reduce waste, and optimize work processes.
- Better decision making: The data-driven decisions provide insights based on actual results rather than assumptions.
- Competitive advantage: The continuous improvement of products, services, and processes helps businesses stand out from their competitors.
- Versatility: A versatile tool for improvement, PDCA can be applied to various business environments and scenarios.
A practical example of PDCA implementation
To illustrate the effectiveness of PDCA, let’s consider a company wanting to reduce the waste produced in its production line.
Plan: The company identifies waste reduction as its primary objective. After analyzing the current situation, it proposes the solution of introducing a recycling system within the production line to reuse waste materials.
Do: The company initially implements the recycling system on a small scale in one of its production lines.
Check: After a set period, the company analyzes the results. It measures the amount of waste reduced, the efficiency of the recycling system and its impact on the production process.
Act: Based on the results, the company decides to implement the recycling system across all production lines. The PDCA cycle begins anew, continually seeking ways to further reduce waste and improve efficiency.
By initially testing on a small scale, the company can assess the effectiveness of a solution before full implementation, reducing potential risks and costs.