How to reduce the emissions of warehouse equipment
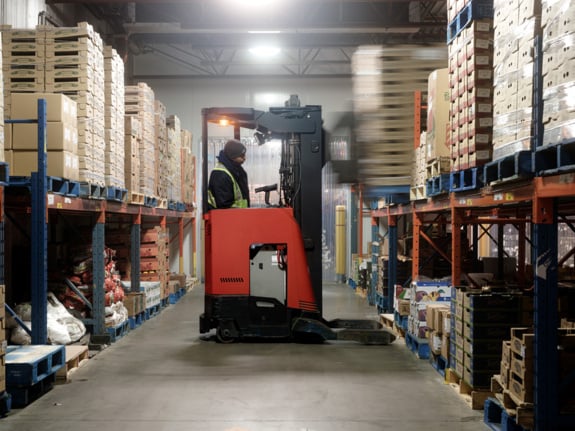
While battery-powered equipment has long been used in warehouses, distribution centres and manufacturing facilities, its popularity has soared in recent years thanks to advances in electric vehicle technology.
Electric forklifts and other material-handling equipment can now do virtually any job that an internal combustion vehicle can do, but with lower operating and maintenance costs, less noise and no direct carbon emissions.
Electric forklifts are increasingly becoming the preferred choice for businesses due to their lower operating costs and environmental benefits.
Choosing the right energy source for your business needs
There are broadly two types of power sources for warehouse forklifts: internal combustion and electric power. Internal combustion forklifts are commonly powered by gasoline, diesel, compressed natural gas (CNG), or liquid-petroleum gas (LPG). However, gasoline and compressed natural gas are not commonly used fuels for warehouse equipment. In cases where they are used, gasoline forklifts refuel like diesel trucks, whereas compressed natural gas trucks need expensive and large refuelling stations.
Electric forklifts require lead-acid or lithium-ion batteries. When evaluating options, it’s important to consider factors such as your operating space, your lifting requirements and your refueling opportunities.
Lifting capacity of internal combustion powered forklifts
Diesel and liquid petroleum gas forklifts have historically been able to lift more than their electric counterparts.
Liquid petroleum gas forklifts lift and move heavy loads over short to medium distances, with a lifting capacity ranging from 3,000 lbs to 15,000 lbs (1,360 kg to 6,803 kg), and sometimes to 20,000 lbs (9,071 kg).
Diesel-fueled forklifts can lift from 3,000 lbs to 40,000 lb (1,360 kg to 18,143 kg), with heavier-capacity models capable of lifting over 125,000 lbs (56,699 kg).
Gasoline and dual-fuel forklifts can lift from 3,000 lbs to 15,000 lbs (1,360 kg to 6,803 kg), with larger models capable to lift heavier loads, while the lifting capacity of compressed natural gas forklifts ranges from 3,000 lbs to 55,000 lbs (1,360 kg to 24,947 kg)
Lifting capacity of electricity-powered forklifts
The lifting power of traditional battery-powered forklifts wanes as their battery gets depleted. However, newer electric machines are maintaining their strength throughout a shift, meaning that the greener option could work for you even if you need to lift heavy loads all day. It all depends on the battery type, which you can read about in the section below.
Refueling for forklifts
Refueling needs for internal combustion forklifts
Diesel-powered forklifts can be refuelled quickly, as long as your staff has the capacity to handle diesel fuel, either at a pump or with gas cans.
Liquid petroleum gas-powered trucks are easy to refuel. The operator simply needs to replace the empty propane canister with a new one, which takes only a few minutes.
As mentioned previously, forklifts that powered using only gasoline are rare due to the popularity of dual-fuel forklifts and the general lack of gasoline fueling stations around warehouses.
Compressed natural gas is better for the environment. However it requires large infrastructure for refueling stations.
Refueling needs of electricity-powered forklifts
Warehouse lifting equipment generally uses one of the following battery types. It’s important to consider these differences when selecting an electric equipment.
Lead acid batteries
The heavy-duty workhorse of the material-handling industry, lead acid batteries have been used in warehouses for a century.
They deliver the greatest amount of power among battery options.
The downside is that they’re not very user-friendly. Their massive weight and extensive handling and maintenance requirements can pose operational challenges and health and safety risks to workers. They also require more dedicated space for recharging.
These batteries lose output power when they’re active. They need to rest and recharge for roughly as long as they’re used. This means they’re not the best option for a business that operates around the clock, unless you plan to buy multiple replacement units.
New lead acid batteries are about 50% efficient
This means only half the electricity that goes into recharging them ends up moving materials. The rest is dissipated during use.
Despite their disadvantages, lead acid batteries remain a viable option for warehouses with shorter job requirements and the space to store, charge and maintain them.
Lithium-ion batteries
Lithium-ion batteries are powering your phone, your laptop and now, more and more, warehouse forklifts.
They don’t lose output power while operating
They can also be opportunity charged, meaning they can be recharged during an operator’s lunch break, for example.
They are safer than sources of power that use combustion
They don’t produce any fumes or the safety and inspection concerns associated with propane and other fossil fuels.
Other considerations for refueling electric forklifts
Battery-powered forklifts require charging stations
Specialized battery storage rooms could even be required in the case of lead acid batteries. Battery chargers range from small units that plug into an ordinary wall socket to equipment that requires large amperage capacities and dedicated wiring. Your facility may require an upgrade in power infrastructure to cope with higher peak demands.
Electric forklifts are limited for work around the clock
Electric forklifts cannot be used for multiple shifts, as they must also be left overnight to charge, which can be inconvenient and slow the production. One solution to limit this constraint is to purchase extra batteries to enable round the clock working, which brings extra expense.
Choose warehouse equipment that is adapted to your operating space
Are the alleys in your warehouse narrow? Does your forklift need to drive over rough terrain? Will your warehouse lift be operating outdoors? Your answers will help you find the equipment that’s right for you.
Internal combustion forklift operating operating details
Diesel warehouse trucks are famous for their torque and ruggedness in all weather and on varied terrain, but they’re also notorious for their emissions. As a result, they generally cannot be used in closed-door facilities or with limited ventilation.
Liquid petroleum gas equipment can be used in well-ventilated indoor spaces because they run on propane, which is much cleaner than diesel.
Gasoline equipment have higher greenhouse gas emissions but lower overall air emissions (i.e. finer particles) than their diesel counterparts. They are still considered as equipment that is only good outdoors.
On the other hand, compressed natural gas forklifts can be used indoors and outdoors due to the lower levels of emissions they produce.
The type of materials handled in your business as indoors versus outdoors use of the equipment also needs to be taken into consideration. With properly maintained forklifts, propane power is usually much cleaner than diesel and can easily be used either indoors or outside. Also, electric- or propane-powered forklifts are strongly recommended in produce-packing and cooling operations to avoid contaminating product.
However, it is important to note that compared to diesel engines, propane-powered engines are not always as performant in extreme cold environments. They are also not entirely emissions-free as they produce carbon dioxide and water vapor.
Electricity-powered forklifts operating details
Battery-powered equipment, emit no emissions and are often the most compact, which makes them the most efficient option for tight indoor spaces. However, electric equipment are generally not the most suitable choice for outdoor use due to temperatures, humidity level and the need for power charging stations at proximity. It is therefore recommended to use them indoors.
Forklifts costs and emissions
Internal combustion forklifts costs and emissions
Vehicles powered by internal combustion may be cheaper upfront, but will cost you more in fuel and maintenance over their lifetimes.
Strictly looking at greenhouse gas emissions, compressed natural gas is the lowest emitting option for internal combustion powered-forklifts, followed by liquid-petroleum gas, then gasoline and finally diesel.
Electricity-powered forklifts costs and emissions
When you buy a battery-powered truck, you’re essentially buying the bulk of its fuel upfront (the battery itself). Despite the higher upfront cost, electric forklifts have a lower total cost of ownership. It is estimated that an electric forklift is 75% cheaper than a propane one. Also, electric forklifts do not release emissions, therefore contributing to lowering your company’s GHG emissions.
To help companies figure out how much they can save by switching to electric forklifts, BC Hydro offers an electric forklift cost calculator. If you’re not in British Columbia, you might need to adjust the cost to match your province.
Comparing energy sources for forklifts
Criteria | Electric | Liquid-petroleum gas | Gasoline | Diesel | Compressed natural gas |
---|---|---|---|---|---|
Environments | Recommended for indoors use and outdoor work in easy weather conditions | Indoor and outdoor | Indoor and outdoor | Outdoor only | Indoor and outdoor |
Lifting capacities | Small to medium | Small to medium | Small to medium | Heavy | Small to medium |
Greenhouse gas emissions | None | Low | High | Medium | Low |
Noise | Low | Medium-high | Medium-high | Medium-high | Low |
Refueling or recharging speed | Lead acid battery: Low Lithium-ion battery: Lower |
High | Medium | Medium | Medium |
Fuel availability | Wide | Medium-wide | Wide | Wide | Low |
Maintenance | Minimal | Regular | Regular | Regular | Minimal |
Market availability | Wide | Wide | Uncommon | Less common | Uncommon |
Total cost of ownership | Higher upfront costs but lower overall costs. Higher upfront costs but lower overall costs. |
Lower upfront, higher overall | Lower upfront, higher overall | Higher upfront, higher overall | Higher upfront, lower overall |
High/medium/low ratings are relative to one another.
Sources: Conger, BDC analysis
How to upgrade to electric warehouse forklifts
1. Evaluate your fleet
The pace at which you convert to electric will depend largely on the condition of your current fleet of forklifts and how you financed them.
If you own your equipment, you may decide to switch over gradually as they wear out. Or you may want to replace the entire fleet if many are nearing the end of their life.
If you lease, you can convert to electric as leases expire.
In planning your transition, remember that operating both internal combustion and electric equipment at the same time will require space and equipment for both refuelling and charging.
2. Line up financing
Using external financing for equipment purchases is a better choice for most companies because it protects your cash flow for day-to-day expenses and unforeseen needs.
“Paying for assets with your own money can put undue financial pressure on your business,” says Trevor Fillo, a BDC Senior Account Manager in Edmonton who finances equipment purchases.
Securing financing before you go shopping allows you to negotiate with vendors from a position of strength.
Fillo notes that leasing your equipment may be the best option for your company, but you should carefully consider the pros and cons before making a decision.
3. Shop around
Study your current use of forklifts to determine the best battery (lithium-ion or lead acid), and size and model for your operation.
Then, take the time to research different suppliers on the market. Read online reviews, ask around and visit trade shows.
Don’t let price alone guide your choice. Check out the reputations of suppliers for quality and after-sales service.
4. Prepare your warehouse for electric equipment
Depending on the battery type you choose, you may need to reserve more floor space for recharging.
This is a good time to optimize your processes to improve your overall floor space and asset utilization.
Next, bring in an experienced commercial electrician to advise you on charging equipment installation and whether you have adequate electrical capacity to meet the additional load or need to upgrade.
5. Train your staff
Like any other important operational change, going electric in your warehouse will require employees to adjust to new ways of doing things. That can be challenging for everyone.
To make the switch as smooth as possible, explain the benefits of electric equipment and why you’re making the change.
Then, ensure they get adequate training and supervision on recharging batteries and maintaining equipment to avoid errors and misuse. Also make sure you are meeting all health and safety regulations.
Implement other energy saving opportunities
Retrofit your warehouse—Warehouses are typically big, open buildings, making them good candidates for an energy saving retrofit that can pay huge dividends.
Install solar panels—The large roof surface of warehouses makes them ideal for being turned into solar farms that can power operations and even feed excess energy into the grid.
Electrify your vehicle fleet—The same arguments in favour of going electric in your warehouse forklifts hold for transportation trucks and vehicles.