Direct costs
Direct costs are the expenses a business incurs to make a product or deliver a service, or when it buys a wholesale product for resale.
Knowing the direct costs involved in operating your company is a key piece of information when it comes to maintaining long-term profitability.
“You absolutely need to know your direct costs. They will tell you where your money is going, giving you an edge when it comes to pricing your goods and services,” says Beth Fisher, Senior Business Advisor, BDC Advisory Services.
She says direct costs will vary as production and purchasing increase or decrease. “They will also fluctuate in response to external factors, such as supplier pricing or currency exchange rates.”
What is the difference between direct and indirect costs?
Direct costs are the expenses a business incurs that are directly tied to a cost object. A cost object is any item for which costs are being separately measured. Indirect costs are the expenses a business incurs that cannot be directly traced to the cost object.
For example, the fuel a salesperson uses to visit his or her clients would be recorded as indirect costs, whereas the fuel used by a transportation company to deliver goods would be a direct cost of that service.
“In other words, indirect costs are not directly related to making a product, providing a service, or buying a wholesale good to resell,” says Fisher. “Consequently, they don’t vary with sales volume, whereas direct costs will vary.”
How to calculate direct costs
With direct costs being numerous and differing from one industry to another, or even from one company to another, there is no single pre-determined mathematical formula to calculate direct costs.
Companies need to analyze all expenses and determine whether or not they are incurred directly in the making of a product or the providing of a service.
“When doing an assessment of a business, we will go through the profit and loss statement—every expense—in order to identify which costs can be classified as direct costs,” says Fisher.
Why calculate direct costs?
Calculating and keeping track of the direct costs involved in operating your company will help improve your profitability.
Pricing is key to business success, and the first step to determine the adequate, profit-generating price for your products and services is to calculate your direct costs. This is because direct costs are a component of the cost of goods sold, which is in turn used to calculate gross profit and gross margin. They also help to determine your break-even point, which occurs when revenue equals total costs (all costs incurred by the company to run its operations).
“Calculating direct costs will help you determine your cost drivers,” explains Fisher. “It will let you know whether you are earning enough profit to cover your overhead and end up with a positive net profit.”
In response to an increase in the price of fuel, for example, a trucking company may need to adjust the per-kilometre rate it charges its customers, since this increase will directly affect gross profits. By doing this, the company would improve its ability to cover all overhead expenses and ensure it maintains a positive net profit.
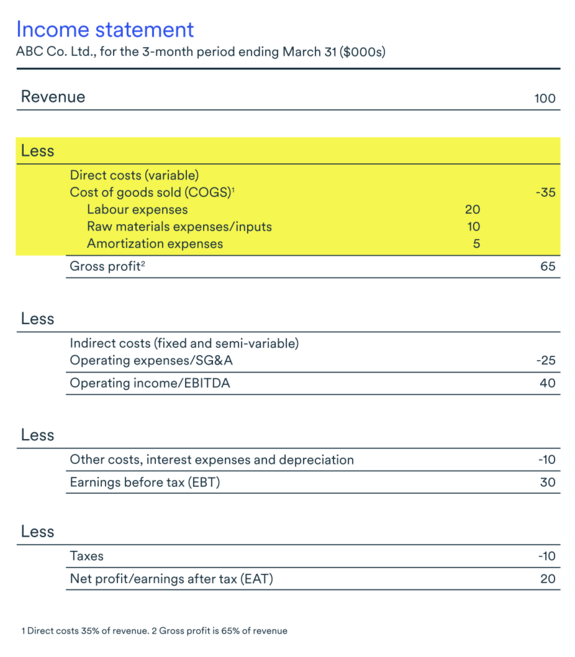
How does a direct cost differ from an expense?
Direct costs are directly tied to revenue: if there are no sales, then no direct costs are incurred. On the other hand, other types of expenses, such as operating expenses, are incurred regardless of sales or revenue.
Office rent, for example, would qualify as an operating expense but not a direct cost, while raw materials would be a direct cost because they’re tied to revenue.
Direct costs affect gross profits; operating expenses affect a company’s net profit.
Examples of direct costs
Businesses tend to incur certain direct costs regardless of the industry in which they operate, such as sales commissions and credit card fees. These costs are only considered direct if they can be tied to a cost object. However, companies’ direct costs usually depend on the industry in which they operate.
Here are some industries and examples of direct costs they incur:
- manufacturing
- direct labour
- raw materials
- manufacturing supplies tied to the product
- fuel or power consumption tied to a facility
- retail
- product purchased for resale
- duties and freight paid to acquire a product for resale
- display and packaging materials
- fees for online ordering platform if directly tied to a product
- services and construction
- direct labour to provide a service
- materials used to provide a service
- rental equipment used to provide a service
- technology and software
- solution implementation support
- customer support—when charged based on usage
- labour for customization of solutions
- trucking and logistics
- fuel
- driver wages
Difference between direct costs, cost of goods sold and cost of sales
Different industries or sectors use different terms to refer to direct costs.
- In manufacturing direct costs are called the cost of goods sold.
- In a retail or wholesale context, a business that buys products from suppliers will typically talk about cost of sales when discussing direct costs.
- In the service sector, the preferred term is cost of service.
Is labour a direct cost?
In certain cases, labour is a direct cost. To be more specific, it is considered a direct cost when it can be tied directly to the cost object, such as a product, service, customer, project or facility. Otherwise, it is considered an indirect cost.
Examples:
- As a direct cost: an employee on an assembly line.
- As an indirect cost: administrative staff.
Is depreciation a direct cost?
Depreciation expenses can be a direct or indirect cost depending on the cost object, as well as how the related asset is used. For example, most manufacturing equipment will represent a direct cost in relation to its department. In this case, the cost object is the manufacturing department. However, manufacturing equipment will most likely represent an indirect cost if the cost object under question is a single unit of production.
“In most cases, depreciation will be an indirect cost to a product or department—the cost object. A portion of the depreciation expense may then be allocated to the cost object,” says Fisher.
She explains that such situations tend to come up mostly in the manufacturing industry. “Say you have an injection moulding machine. The depreciation expense is directly tied to that department. It will then be allocated to the products produced using that machine in that department.”
Next step
Discover how to analyze your business' financial information by downloading the free BDC guide, Build a More Profitable Business.